在制造业中,如何通过系统化的策划让产品从设计到量产都“一次做对”?答案藏在一种名为APQP的管理方法中。本文将深入解析这一工具的核心逻辑,并为企业提供可落地的实践指南。
一、APQP的本质:提前填平产品开发的“坑”
APQP(Advanced Product Quality Planning)即先期产品质量策划,是一种贯穿产品全生命周期的结构化方法。它要求企业在产品开发的早期阶段,就对可能影响质量的环节进行系统性规划,从而减少后期变更、降低成本,并确保产品符合客户期望。
核心逻辑:
预防优于纠正:通过设计验证、风险评估等工具,提前发现80%的潜在问题。
跨部门协作:工程、生产、采购、质量等部门形成“同步工程”机制,打破信息孤岛。
阶段化控制:将开发过程拆解为可管理的五个阶段,每个阶段都有明确的输入输出标准。
企业常见误区:
认为APQP只是“填写表格”,忽视其对风险的前瞻性识别。
将APQP局限于质量部门,未实现全员参与。
二、APQP五阶段实施详解(附实用工具清单)
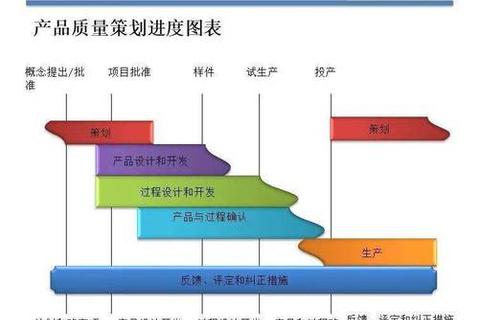
阶段1:项目启动与需求锁定
关键动作:组建跨职能小组(建议包含客户代表)、进行QFD质量功能展开、输出可行性报告。
工具推荐:客户需求矩阵表(明确功能、性能、法规要求)、SWOT分析(评估企业资源匹配度)。
阶段2:产品设计与验证
核心任务:完成DFMEA(设计失效分析)、样件制作、材料规范制定。
避坑指南:某汽车连接器企业案例显示,在此阶段未充分验证端子插拔寿命,导致量产后退货率高达15%。
阶段3:过程设计与开发
重点输出:PFMEA(过程失效分析)、试生产控制计划、测量系统分析(MSA)方案。
实用技巧:用流程图可视化生产过程,标注关键控制点(如焊接温度±2℃的精度要求)。
阶段4:产品与过程确认
必做事项:完成PPAP(生产件批准程序)、过程能力指数CPK≥1.33、包装运输测试。
数据陷阱:某电子厂因忽略量具重复性误差(GRR>30%),误判过程稳定性,损失超200万元。
阶段5:量产与持续改进
管理要点:建立SPC控制图监控关键参数、实施PDCA循环优化。
创新实践:某家电企业通过大数据分析售后故障数据,反向优化设计标准,使产品寿命提升30%。
三、APQP成功落地的四大关键策略
策略1:建立“铁三角”协作机制
角色分工:项目经理(统筹进度)、质量工程师(风险预警)、工艺工程师(技术落地)。
会议管理:每周召开跨部门站会(建议使用看板管理工具),重点跟踪高风险任务。
策略2:用数字化工具提效
推荐系统:PLM(产品生命周期管理)系统集成APQP模块,实现文档自动归档、节点预警。
数据分析:通过Minitab进行过程能力分析,快速识别异常波动点。
策略3:分层培训体系搭建
管理层:侧重APQP战略价值认知(案例:某企业将APQP执行率纳入KPI,项目准时交付率提升45%)。
工程师:培训FMEA、控制计划等工具实操(建议采用沙盘模拟形式)。
策略4:供应商协同管理
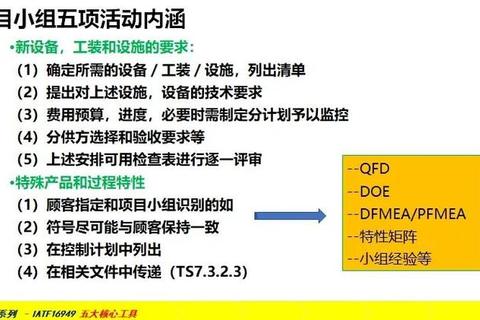
早期介入:要求核心供应商参与设计评审,特别是材料选型环节。
能力评估:使用VDA6.3过程审核标准,重点考察模具维护、变更管理能力。
四、行业应用场景与特殊注意事项
汽车行业(典型应用)
特殊要求:必须通过AIAG五大工具认证,PPAP提交需包含IMDS材料数据。
最新趋势:新能源车线束开发中,APQP阶段需增加高压绝缘测试、EMC兼容性验证。
消费电子行业
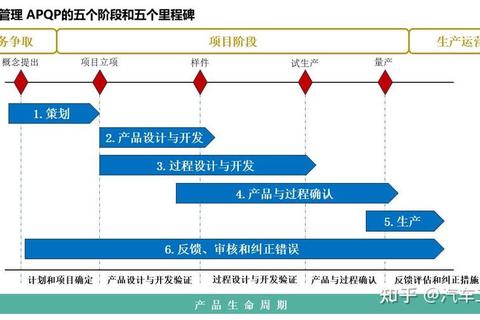
敏捷适配:在快速迭代项目中,可将APQP阶段合并(如将阶段2-3并行执行),但需加强风险评审频次。
成本控制:通过DFMA(面向制造与装配的设计)优化结构,某手机厂商将组装工时降低20%。
医疗器械行业
合规重点:设计验证必须符合ISO13485标准,生物相容性测试需在阶段3完成。
文档管理:所有APQP记录需保存至产品生命周期结束后2年,应对FDA审计。
五、从理论到实践:给企业的三条速效建议
1. 启动试点项目:选择复杂度中等的产品线试行APQP,积累经验后再全面推广(建议周期3-6个月)。
2. 建立Checklist机制:制定各阶段交付物检查清单(如阶段4必须完成10项测试报告),减少人为遗漏。
3. 量化收益看板:跟踪关键指标(如工程变更次数下降率、客户投诉率),用数据说服团队。
通过系统化的APQP实施,企业不仅能避免“量产即灾难”的窘境,更能在产品竞争中获得差异化的质量优势。正如某世界500强企业质量总监所言:“APQP不是成本,而是对未来收益的投资。”